The Hero, Nobody, Talks About How Multistage Pump Repair Keeps Industries Flowing Smoothly
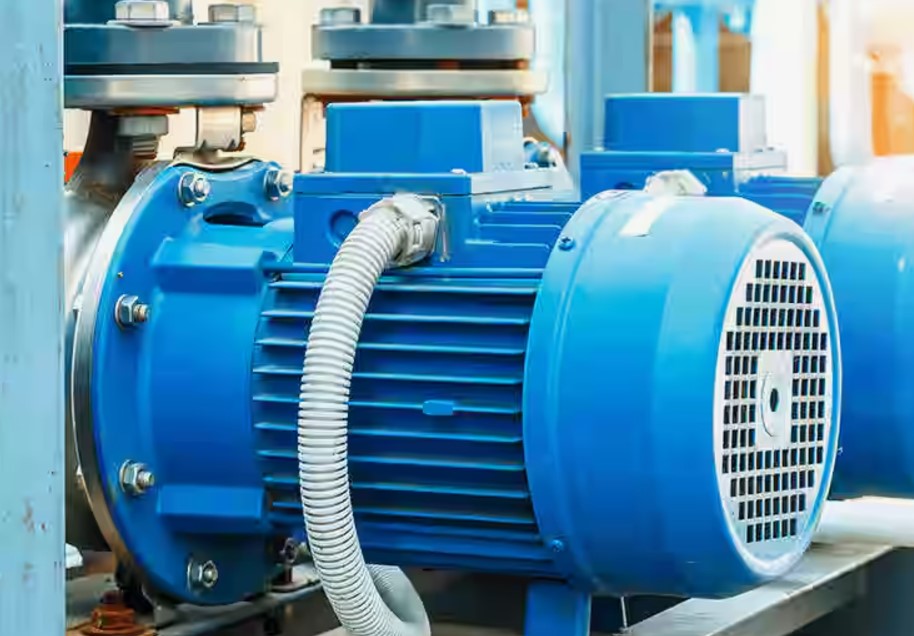
In the world of industrial machinery, there’s a silent hero that often goes unnoticed despite playing a critical role in powering factories, refineries, and power plants around the globe: the multistage pump. Designed to deliver exceptional pressure and reliability, multistage pumps are indispensable in industries where high-pressure fluid transport is a must. And yet, their significance is seldom recognized—especially when it comes to the maintenance and repair that keep them running efficiently.
While multistage pumps are designed to be durable, even the best machines require regular care. Multistage pump repair is an art and science that ensures these quiet heroes perform at peak efficiency, reduce downtime, and deliver significant cost savings. Here, we’ll dig deeper into the vital role of multistage pump repair, why it’s often overlooked, and how its benefits extend beyond just the machines themselves.
Why Multistage Pumps Are the Backbone of Industry
Multistage pumps are built to manage high-pressure applications using multiple impellers—each stage or impeller adds energy to the fluid, increasing pressure. This makes them ideal for tasks that require a steady flow of pressurized liquid, such as in desalination plants, boiler feed systems, and mining operations. These systems can handle everything from freshwater to abrasive slurries, making them versatile in high-stakes environments.
A well-maintained multistage pump can run continuously for years without issue, but neglecting repairs can have costly consequences. Multistage pump repair ensures these pumps meet pressure demands, maintain operational efficiency, and avoid unexpected shutdowns.
The Unspoken Costs of Ignoring Repair for Multistage Pumps
The significance of routine maintenance is sometimes overlooked, particularly when a multistage pump is operating efficiently. However, neglecting maintenance can have serious unintended consequences. Industry reports indicate that an out-of-calibration pump can use up to 30% more energy than needed. Furthermore, a single incident of unplanned downtime brought on by a pump failure might result in emergency repairs and lost production of tens of thousands of dollars.
According to research by the Aberdeen Group, unplanned downtime costs industrial businesses an average of $260,000 every hour. Pumps utilize around 20% of the world’s energy, particularly in energy-intensive industries; therefore, the financial effects of ignored maintenance must be addressed. Regular multistage pump repair helps to avoid these financial pitfalls and keeps operations flowing smoothly.
When to Consider Multistage Pump Repair
The signs that a multistage pump needs repair can be subtle. Operators should look out for specific issues that indicate maintenance is required. Key red flags include:
Reduced Flow and Pressure: A decrease in output pressure or flow rate often indicates that wear affects performance.
Increased Energy Consumption: When a pump struggles to operate at its designed efficiency, energy usage often rises as it tries to compensate.
Unusual Sounds and Vibrations: Changes in sound or increased vibrations can indicate issues with bearings, impellers, or shaft alignment, which require immediate attention.
Leaks or Seal Failures: A leak can indicate a worn-out seal or gasket, which, if ignored, could lead to further mechanical failures.
Being proactive and scheduling multistage pump repair at the first sign of trouble can save companies time and money and prevent unplanned outages.
The Multistage Pump Repair Process: Restoring Efficiency
Multistage pump repair involves more than just fixing broken parts. The process is detailed and precise, restoring the pump’s original efficiency. Here’s an overview of the typical repair procedure:
Diagnosis and Inspection: Technicians first perform an in-depth analysis of the pump’s condition, examining components like impellers, seals, bearings, and shafts. This inspection is critical for identifying areas of wear and potential failure.
Disassembly and Cleaning: Once the problem areas are identified, the pump is disassembled, and each component is meticulously cleaned to remove any buildup that might interfere with performance.
Component Replacement or Repair: Damaged parts, such as worn impellers or seals, are either repaired or replaced. Components are tested for wear and alignment to ensure compatibility and performance.
Reassembly and Calibration: The pump is reassembled and calibrated after replacing parts. This step is essential for ensuring that it meets its performance requirements.
Performance Testing: The final step is rigorous performance testing to ensure the repaired pump operates at peak efficiency before reinstalling.
This thorough process ensures the pump is in top working condition, ultimately enhancing performance, efficiency, and lifespan.
Benefits of Regular Multistage Pump Repair and Maintenance
Multistage pump repair isn’t just about fixing problems—it’s an investment in efficiency, safety, and sustainability. Here’s how:
Increased Operational Efficiency: Regular repairs keep multistage pumps running optimally, maximizing flow rates and pressure while reducing energy consumption.
Reduced Downtime: Proactive maintenance prevents costly breakdowns and the lost productivity of unplanned shutdowns. According to a McKinsey report, predictive maintenance could reduce equipment downtime by 30-50%.
Cost Savings: When pumps operate efficiently, they consume less energy, lowering energy bills. The Department of Energy states that even minor inefficiencies in industrial equipment can increase costs significantly over time, making regular repair a sound financial choice.
Environmental Impact: Optimizing pump performance reduces energy waste, lowering industry carbon footprints. Since industrial pumps contribute substantially to global energy usage, reducing power consumption is an economic and ecological imperative.
Technology and the Future of Multistage Pump Repair
Advancements in technology are transforming the approach to multistage pump repair. Today, IoT sensors and advanced diagnostics make it possible to detect problems before they lead to breakdowns. These technologies continuously monitor pump performance, identifying issues such as wear or imbalance early so that repairs can be scheduled proactively.
Additionally, digital twin technology allows technicians to create a virtual pump system model, simulating different scenarios to understand performance without physical interference. This model-driven approach enhances repair accuracy, reduces costs, and minimizes downtime.
In one case study, a major oil and gas company leveraged IoT sensors to monitor their multistage pumps, resulting in a 20% reduction in maintenance costs and a 15% increase in operational efficiency. This example underscores the value of incorporating modern technology into multistage pump repair.
Conclusion: Recognizing the Unsung Hero
Multistage pumps may not make headlines, but their indispensable role in the industry is undeniable. These heroes face an uphill battle without proper maintenance, impacting operations and the bottom line. Multistage pump repair isn’t just a technical necessity—it’s a strategic decision that drives efficiency, reduces costs, and safeguards the environment.
So, the next time you walk by a humming industrial pump, take a moment to appreciate the quiet hero that keeps industries running smoothly. Through dedicated maintenance and repair, we can ensure that these unsung heroes continue to perform, proving that sometimes, the strongest assets are the ones that operate silently in the background.
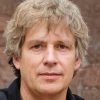
Biker, shiba-inu lover, guitarist, Swiss design-head and multidisciplinary designer. Performing at the fulcrum of aesthetics and programing to create not just a logo, but a feeling. Let’s design a world that’s thoughtful, considered and aesthetically pleasing.
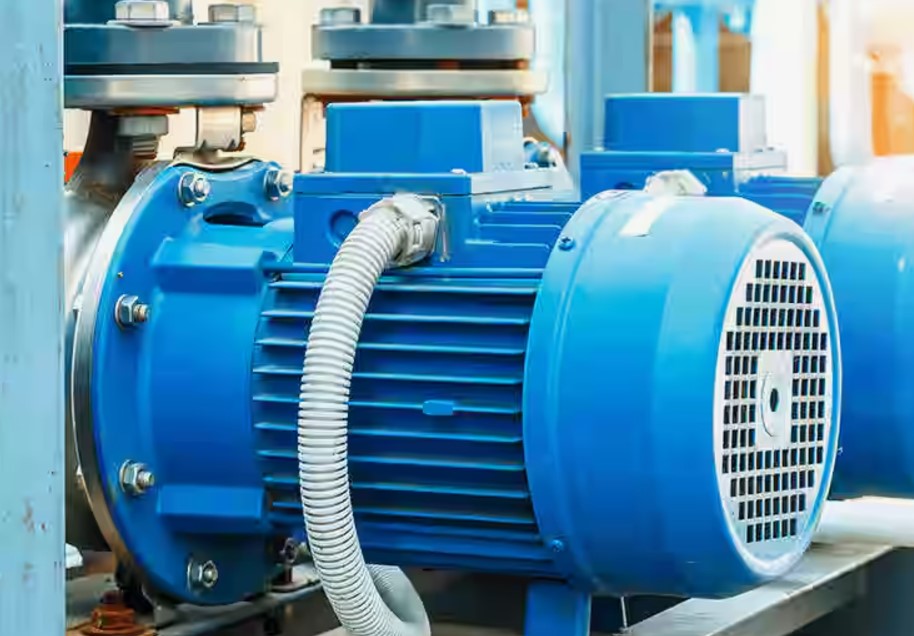